The production halls are equipped with adjustable energy-saving lighting with different light levels and light spectra. In addition, a light barrier has been installed, which makes it possible to raise the poultry under various light conditions. The microclimate in the production halls is regulated by Fancom computers with the parameters set in them for poultry keeping, according to the recommendations for the COBB cross. The air in the production facilities is humidified by a fine mist of water, using nozzles, through a Lubing high-pressure pump. Heating is zoned by temperature sensors - gas generators, manufactured by the Dutch company ESTEL.
One of the main activities of AGROSILA Holding is the introduction of advanced technologies into production processes. All of the companies within the holding company are implementing an extensive program of innovative developments in order to improve production technology and product quality.
Chelny-Broiler is currently an innovative poultry complex, one of the largest chicken meat producers in Russia and a leader in the Volga region. Chelny-Broiler's products meet the highest requirements and international quality standards. The high quality of the products is achieved not only through full compliance with technological processes, but also through the use of innovation, as well as the use of the most modern high-performance equipment.
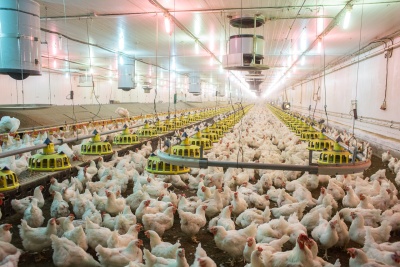
The production halls are equipped with adjustable energy-saving lighting with different light levels and light spectra. In addition, a light barrier has been installed, which makes it possible to raise the poultry under various light conditions. The microclimate in the production halls is regulated by Fancom computers with the parameters set in them for poultry keeping, according to the recommendations for the COBB cross. The air in the production facilities is humidified by a fine mist of water, using nozzles, through a Lubing high-pressure pump. Heating is zoned by temperature sensors - gas generators, manufactured by the Dutch company ESTEL.
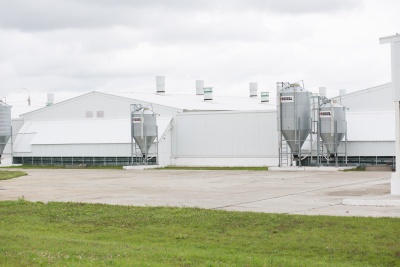
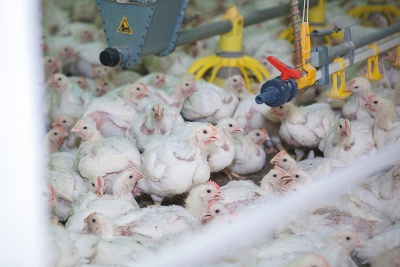
The poultry are fed using the feeding lines of "Roxell", the world's leading manufacturer of automated feeding and watering systems for industrial poultry farming. The poultry are watered via nipple bowl drinkers with water pressure regulators.
The company uses the technology of rapid or shock freezing of products. Compared to the traditional method, this technology makes it possible to freeze products in a short time to a temperature of -18C. During such freezing, ice crystals are formed at a much smaller size and almost simultaneously in the cell and intercellular septa (cells remain undamaged). As a consequence, the structure of the tissues remains virtually unchanged. This keeps the product fresh and avoids water release when defrosting the meat.
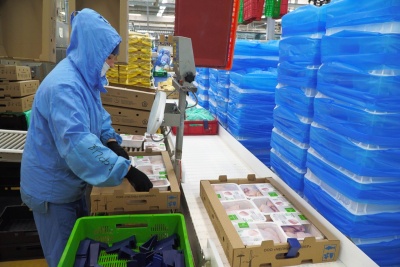
The company uses vacuum packaging and packaging in a gas-protective environment, which extends the shelf life and preserves the taste of products. At the same time, the product is attractively packaged and has its original appearance throughout its shelf life due to the lack of moisture exchange.
Chelny-Broiler LLC has acquired one of the innovations in global practice: a product packaging machine: carcass in vacuum. This technology eliminates operator contact with the product during packaging due to the absence of cross-contamination. The vacuum also prevents the growth of micro-organisms that live in an oxygenated environment - thus doubling the shelf life of the product. The packaging of the dressed carcass technology also aims to produce a safe and fresh product with maximum shelf life - it is a product in a gas environment. This technology removes oxygen from the packaging.
One of the main activities of Agrosila Holding's agricultural companies is the production of livestock products. To achieve high milk yields, specialists at the holding company have developed an original keeping and feeding technology. It provides for year-round stabling of animals in open complexes with comprehensive feeding rations and veterinary care, thus avoiding seasonal fluctuations in milk and meat production.
All of the holding's cattle breeding complexes are equipped with modern milking, cooling and feed preparation and distribution equipment. This makes it possible to automate key production processes and achieve high quality milk and meat at minimal cost.
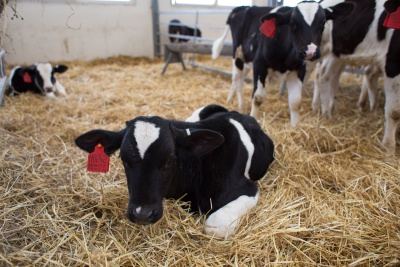
All agricultural companies are actively working to improve the breed qualities of cattle by using frozen semen of bulls with maternal cow productivity of at least 8,000 litres of milk per lactation. To this end, agricultural companies cooperate with breeding companies that provide artificial insemination points of farms and complexes with high-quality bull semen of American and domestic breeding stock, as well as consumables.
The agricultural companies have adopted European insemination technology. Artificial insemination coverage of breeding stock is over 70%. High-quality breeding stock is purchased.
Training for livestock breeders and reproduction technologists is provided on a regular basis with the involvement of specialists from leading breeding companies and livestock breeding organizations. The dairy farms have personal computers equipped with the latest CELEX and Alpro system software to keep breeding records.
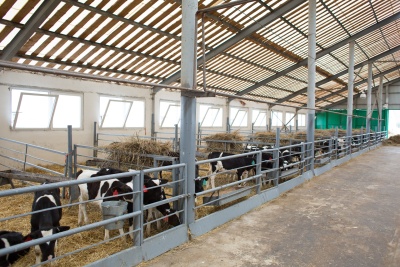
In order to organize veterinary and sanitary and therapeutic and preventive measures in cattle breeding and livestock production, the holding company has established a veterinary service structure that works closely with the Federal State Institution Tatar Interregional Veterinary Laboratory, Biofram Company LLC and the district state veterinary associations.
Its main task is to organize and carry out measures to prevent animal diseases and fatalities, the purpose of which is to increase the number of livestock and its productivity, to provide the population with high-quality livestock products with the least amount of labor and money.
Veterinary activities on dairy complexes are carried out by veterinarians and veterinary treatment operators for animals and premises. The veterinary service at each dairy complex has its own material and technical base. Specialists are equipped with all the necessary equipment and the latest veterinary drugs for the prevention and treatment of cattle. A range of measures to eliminate cattle leukaemia is implemented in the agricultural holding company. Each complex has an equipped bio-thermal pit for the disposal of biological waste.
The holding company established hoof treatment and rectal examination teams with ultrasound scanners for cows and heifers, which increased the efficiency of livestock breeding by reducing culling and service period. A method of diagnosing blood sugar and ketone bodies in dry and newborn cows has been developed and implemented. Veterinary practitioners have also introduced refractometers - devices for determining immune bodies in the blood of newborn calves - into active use on farms.
The holding company uses the latest immunoprophylaxis schemes from birth to adult livestock.

The transition to modern feeding systems is profitable by increasing milk productivity, improving animal health and reproduction, as well as reducing feed wastage.
The livestock's own fodder supply is provided by the harvesting of rough and succulent grasses. Technological processes are mainly carried out using equipment from leading global manufacturers. High technical equipment, harvesting of fodder grasses in optimal time allows preparing high quality fodder in large volumes.
The use of premixes and feed additives is widespread in agricultural companies and has increased the marketability of milk to 96-98%. The use of premixes makes the rations of cows and young cattle more nutritious. Fodder quality is analyzed by the farms in the production laboratory, which allows feed rations to be calculated according to their actual nutritional content.
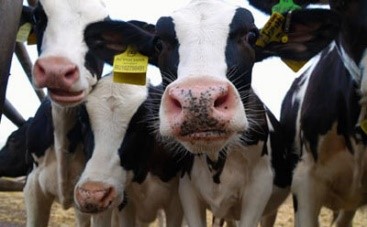
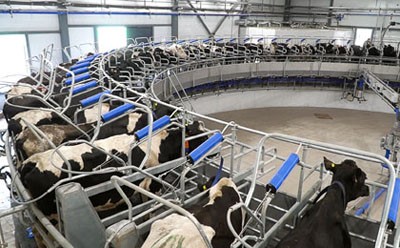
- Power BI (Business Intelligence system)
- Dairy Production Analytics, which allows real-time access to up-to-date data, analysis and monitoring of key indicators, timely notification of deviations, and reliable forecasts.
- CELEX, which allows you to create a closed cycle of information processing for cattle on the farm.
- Dairy feeder, managing the feeding process.
- Dairy Comp, responsible for herd management.
Today, AGROSILA Holding is one of the largest landowners in Russia. All of the agricultural companies are producers of high-quality organic products. Progressive resource-saving cultivation technologies are used on the agricultural holding's fields, and crop rotations with sideral pairs are organized to increase soil fertility and reduce the use of mineral fertilizers. High-margin agricultural crops such as sugar beet, oilseed rape and lupine are cultivated. Plant growth stimulants and micronutrients are widely used in seed inoculation and during vegetation.
The technical base of the agricultural holding, which is annually replenished and updated, deserves special attention. It includes a fleet of new and advanced agricultural machinery from well-known companies such as New Holland, Hatzenbichler, Farmet, Kwernelland, Quivogne, Jaguar, Claas, Case, Lemken, Amazone, John Deere, Kuhn, Horsch Holmer, McCormick, Challenger.
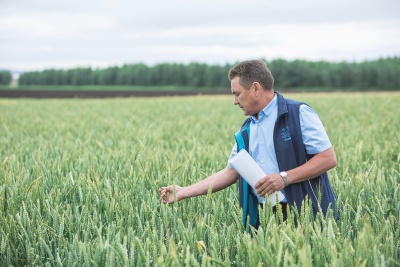
The seed plant is a new step in the development of the holding company's crop production. Agricultural company Kama LLC's seed plant is the largest seed plant in Russia. The capacity of the unique seed plant reaches 40 tons of grain per hour in calibration. The main types of products produced by the company are original, elite and first reproduction seeds of grain and leguminous crops.
The seed plant provides the holding's agricultural companies with high-quality seeds and improves the quality of their products while reducing production costs through the use of modern, advanced technology, which allows for the proper selection of varieties adapted to a particular farming area through competitive varietal testing. At the same time, the yield of grain crops increases by 5-7 cwt / ha. The company has its own variety-testing fields, where more than 100 types of promising varieties are tested.
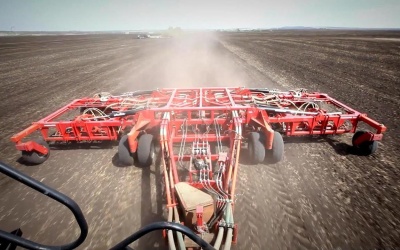
The no-till technology eliminates the use of the plough, which destroys soil structure and leads to soil erosion, reduced biohumus levels and, consequently, lower fertility. Instead, disc harrows, different types of cultivators, deepeners that improve soil structure and wide-cutting equipment are used to reduce the number of passes over the field and thus reduce costs per hectare of cultivated area. Simultaneously with cultivation, sowing is done in one pass, which also reduces the cost per hectare. This technology allows for proper crop rotation with the use of green manure crops (rapeseed, colza). This reduces the use of mineral fertilizers and crop protection products and improves soil fertility.
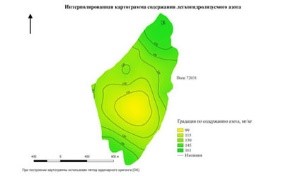
AGROSILA was one of the first companies in Russia to introduce innovative precision farming technology. Investments in differentiated fertilizer application based on the results of agrochemical soil survey amounted to 3.2 million rubles. The project has already ensured:
- reduction of fertilizer costs by not applying fertilizer in areas of the field with sufficient availability (for example, in field 42008, with an area of 153 ha, an economic effect of 480,000 rubles excluding VAT was obtained by reducing the amount of ammophos applied);
- higher yields through optimum use of fertilizers.
In the future, deeper integration with machinery is planned, including online interaction, remote data exchange for downloading application maps and uploading application results.
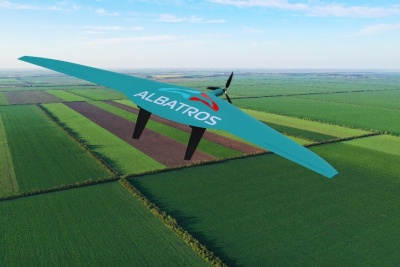
- the time required to prepare and update maps has been reduced;
- the basis for further implementation of precision farming technologies and use in other systems (business intelligence, machinery monitoring and accounting system) has been created;
- it is now possible to create thematic maps with a clear representation of the data and the necessary analytics (crop rotation, agrochemical soil analysis data, UAV overflight results, NDVI index, crop yields, etc.);
Used in crop production and IOT (Internet of Things). The implementation of the project has already minimized the workload of the staff in charge of the monitoring function thanks to the automatic data processing mechanisms that have been developed. Monitoring is carried out remotely by the monitoring centre. As a result of the system implementation, the following results have been achieved:
- a mechanism for monitoring the operation of grain harvesting equipment during the harvesting campaign has been implemented, over 250 harvesters are being monitored (including unloading of grain) by just one staff member;
- monitoring the speed of machinery during agricultural operations;
- calculation of the cultivated area based on the machine's activation data;
- automatic detection of work in "foreign" areas.
Future plans include deeper integration with machinery, receiving machine data via ISOBUS and transmitting it remotely, and using machine learning technology to move towards fully automatic control.
Today, the Zainskiy Sugar factory is one of the most powerful production sites in Russia. High production indicators have been achieved, among other things, thanks to the introduction of advanced technologies in sugar beet cultivation, processing, harvesting and storage. In addition, the company has introduced the Agro Production System, based on the Lean Production system, which in turn also helps it to achieve its goals.
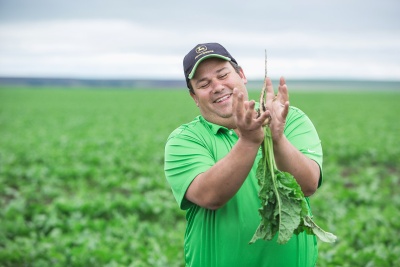
AGROSILA Holding is one of the first companies in Russia to introduce the innovative Amity sugar beet cultivation, processing and harvesting technology. The main advantage of the new technology is the ability to take advantage of rather harsh climatic conditions. The difference with this technology is that the row spacing in the crops is 56 cm instead of 45 cm. The weeds are eliminated mechanically and herbicides are only applied to the crop rows. This reduces costs and the pesticide load, resulting in cleaner fields. And the sugar content of the root crop increases due to spot application of liquid fertilizers and leaf dressing. In total, the new system increases the harvesting rate by 24%.
To implement the project, Amity Technology's state-of-the-art, high-capacity agricultural machinery was purchased to help reduce costs and increase yields. Foreign specialists were invited to train the employees of the holding.
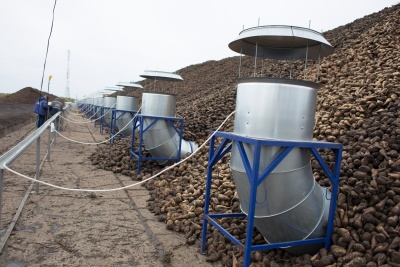
In order to increase the storage time of sugar beet, the holding has created a state-of-the-art system of pile fields. Innovative industrial cooling and ventilation equipment has been installed at the Zainskiy Sugar factory. With the new technology, the beet storage period is increased from 4 to 6 months. This system thus makes it possible to unify technological processes, as well as to minimize losses during storage of root crops almost twice.